Logistyka – ciągłość działania oczami praktyka
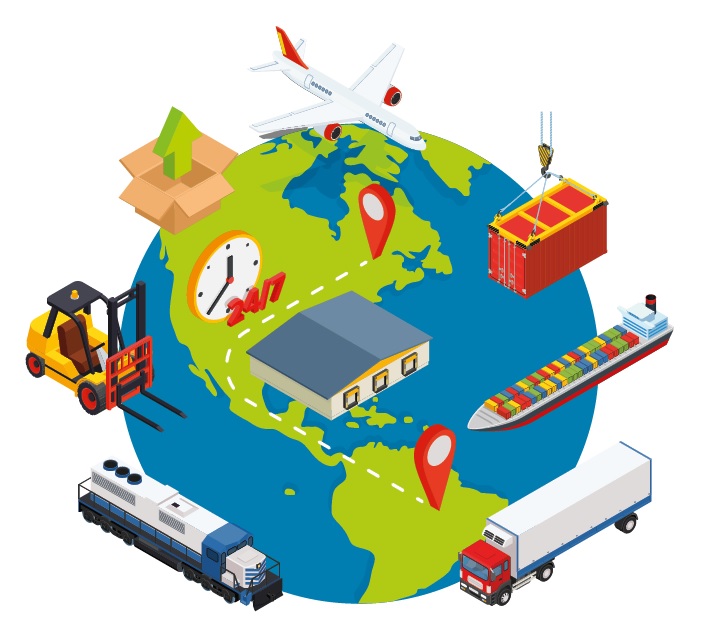
Jacek Grzechowiak
Logistyka jest elementem, bez którego trudno sobie dzisiaj wyobrazić funkcjonowanie organizacji biznesowych. Bez sprawnej logistyki niemożliwe jest także efektywne zarządzanie kryzysowe.
Opracowano wiele norm i standardów dotyczących zarządzania procesami logistycznymi, m.in. normy z serii ISO 28001), a także ISO 90012), 140013), 223014), 223015), 270016), 450017) oraz standardy C-TPAT8) czy AEO9). Należy mieć na względzie także normę ISO 3700110) – jedną z serii norm dotyczących ryzyk współcześnie szczególnie obecnych. Dlatego postanowiłem spojrzeć na zagrożenia dla ciągłości procesów logistycznych przez pryzmat incydentów z pozoru niemających wpływu na bezpieczeństwo i ciągłość działania.
W ciągłości działania nie ma rzeczy nieważnych. Ludzie, systemy, mienie, otoczenie, pogoda, a także kryzysy dotykające innych branż (jak to miało miejsce w przypadku firmy Victorinox11)) – każdy rodzaj aktywności biznesowej ma na to wpływ. Może on być krytyczny, a jego znaczenie nie zależy od żadnych stałych.
Pojęcie constans tu nie istnieje.
Czynnik ludzki – zdrowie i jego potencjalny wpływ na ciągłość działania
Ptasia grypa, świńska grypa i… SMS-y z urzędu
Ptasia grypa i temu podobne epidemie wydają się już „przećwiczone”. Na szczęście nie doświadczyliśmy krytycznych zagrożeń, chociaż w czasie pierwszego alarmu związanego z ptasią grypą wiele firm borykało się z prozaicznym problemem zidentyfikowania ptaków ją roznoszących, a nakłonienie pracowników do proceduralnego mycia rąk napotykało problemy. Tymczasem ćwiczenia symulacyjne, dotyczące potencjalnego wpływu dowolnej infekcji rozprzestrzeniającej się selektywnie (np. w jednym dziale czy jednym oddziale terenowym) ujawniały destrukcyjny wpływ na funkcjonowanie organizacji (casus firmy Victorinox).
Tutaj także, wzorem case study Victorinox, kłopot podwykonawcy może w efekcie dotknąć nas, w postaci przerwy w dostawie komponentów produkcyjnych, czy zaburzeniu transportu wyrobów (zwłaszcza w firmach, potrzebujących specjalistycznych środków transportowych). Zjawiska te zachęcają przedsiębiorców do stosowania zaawansowanych działań prewencyjnych zarówno w zakresie opieki medycznej, jak i kształtowania odpowiednich postaw dotyczących higieny i reagowania na symptomy choroby (nawet tak z pozoru niegroźnej, jak katar). Prewencja to oczywiście nie wszystko. Coraz częściej spotykane podwójne specjalizacje pracowników są także narzędziem zarządzania tym ryzykiem.
W ostatnim czasie pojawiło się jeszcze jedno zagrożenie mogące skutkować masową absencją. Jest nim rozsyłanie fałszywych SMS-ów, jak to miało miejsce jesienią ub. roku na terenie województwa podkarpackiego12). Nie wdając się w szczegóły, czy to tylko techniczna pomyłka, czy realny przypadek zagrożenia hybrydowego, można sobie wyobrazić potencjalne skutki selektywnego wystąpienia takiego ryzyka. Dziś bowiem coraz więcej firm ma do dyspozycji serie numerów telefonicznych dla swoich pracowników. To wygoda, ale i ryzyko – przy serii numerów selektywne zaatakowanie danej firmy jest dużo łatwiejsze.
Negatywny wpływ tego ryzyka jest bezsporny i wymaga podjęcia działań prewencyjnych. Należą do nich bi-, a nawet multispecjalizacja pracowników pozwalająca utrzymać ciągłość działania w przypadku nasilonej lub masowej absencji. Innym narzędziem może być procedura potwierdzania alarmu wymagająca, co oczywiste, zbudowania odpowiedniej ścieżki powiadamiania – od osób otrzymujących powiadomienie do struktury czy osoby odpowiedzialnej za weryfikację alarmu i przekazanie informacji zwrotnej pracownikom. W tym obszarze z pewnością będziemy mogli zdobywać doświadczenie w zarządzaniu tym ryzykiem.
Czasem bywa jednak jeszcze gorzej
Czynnik ludzki z natury jest jednym z najbardziej nieprzewidywalnych w zarządzaniu, szczególnie jeśli chodzi o zdrowie pracowników podmiotów zewnętrznych, na które jako szefowie bezpieczeństwa nie mamy żadnego wpływu. Musimy uwzględniać stany wyłączające osoby z aktywności zawodowej długotrwale i na stałe. Takie ryzyko może mieć także negatywne konsekwencje dla stanu bezpieczeństwa.
Wyobraźmy sobie przejezdną halę magazynową. Wjazd z jednej strony, wyjazd z drugiej – rozwiązanie jakże często spotykane. Zablokowany w takim miejscu pojazd powoduje wstrzymanie załadunków w sposób oczywisty. Wstrzymanie załadunków skutkuje opóźnieniem wysyłki, a co za tym idzie opóźnieniem dostaw towarów do miejsc ich przeznaczenia. Czy tylko tym?
Powierzchnia magazynowa ma swoje ograniczenia. W przypadku produkcji ciągłej wstrzymanie załadunków może skutkować nawet koniecznością wstrzymania produkcji, a to już problem bardzo poważny. Nagła choroba kierowcy i konieczność udzielenia mu pierwszej pomocy, a niekiedy użycia specjalistycznej aparatury (np. defibrylatora) czy też wezwania pogotowia ratunkowego – to wszystko powoduje oderwanie innych od pracy i wstrzymanie procesów logistycznych. Może pojawić się też problem z uruchomieniem pojazdu – z reguły krótkotrwały, chyba że kierowca straci przytomność. Wtedy pojawiają się komplikacje wydłużające proces rozwiązania problemu. Uruchomienie pojazdu przez osobę trzecią wcale nie musi być proste (nie wiadomo, czy pojazd ma blokady zapłonu, jakie, kto zna kody itd.).
W przypadku zgonu kierowcy komplikacje stają się poważne, niezbędne jest bowiem wezwanie nie tylko pogotowia, ale także policji (być może prokuratora, jeśli policja podejmie taką decyzję) i zakładu pogrzebowego. Wszystko to powoduje zablokowanie strefy zdarzenia nawet na 4 godziny. To długi czas, jego negatywny wpływ może być poważny. Można oczywiście budować dalsze „czarne scenariusze” typu noc, brak zasobów itd., ale nie o to chodzi. Celem jest uwrażliwienie na problem, z pozoru neutralny, mogący jednak przynieść poważne szkody.
Oczywiście uniknięcie takich incydentów nie jest możliwe, ale reagowanie w przypadku ich wystąpienia może zostać zaprogramowane. Rozwiązania znane np. z bezpieczeństwa podróżowania mogą stanowić pomoc w zapobieganiu takim zagrożeniom i zarządzaniu incydentami. Mowa o dwóch prostych narzędziach ułatwiających reakcję w przypadku takich incydentów. Są to:
• podróżna karta zdrowia (travel safety card),
• karta użytkownika pojazdu.
Oba dokumenty pomagają przyspieszyć reagowanie. Wiemy, jakich lekarstw przyjmowanych przez kierowcę szukać w pojeździe, gdyby trzeba było je pilnie podać, mamy też dostęp do danych kontaktowych właściciela pojazdu (lub dyspozytora), który może pomóc w usunięciu pojazdu z miejsca załadunku. Żaden z tych dokumentów wprawdzie nie zapobiegnie incydentowi, ale może pomóc zapobiec eskalacji problemu.
Istotne jest także współdziałanie struktur bezpieczeństwa i BHP, pozwalające osiągnąć synergię w prewencji i reagowaniu na incydenty. Takie rozwiązania obserwuję coraz częściej, co potwierdza tezę, że współpraca tych struktur ma głęboki sens.
Podobne ryzyka będą występowały w przypadku awarii technicznych pojazdów w miejscu załadunku. Będą one nieco mniej dolegliwe, gdyż nie będzie potrzebna interwencja policji czy pogotowia, ani konieczność zamknięcia strefy zdarzenia, a i kierowca będzie w stanie aktywnie uczestniczyć w zarządzaniu incydentem. Jednak i w tym przypadku określona procedura przyspiesza rozwiązanie problemu.
IT: „nie wasza sprawa”…
Czyżby?
Systemy informatyczne są dziś nieodzowne właściwie wszędzie. Jednocześnie informatycy dość mocno strzegą dostępu do „ich królestwa”, co sprawia, że szef bezpieczeństwa rzadko wie w szczegółach, co zachodzi w świecie bitów i bajtów – z reguły do czasu, aż bity i bajty nie spowodują incydentu, za co odpowiada już szef bezpieczeństwa. Wtedy koleżanki i koledzy z IT bardzo chętnie przekazują mu sprawę, zastępując zwrot „nie twoja sprawa” zwrotem „nie moja sprawa”. Można by powiedzieć: samo życie.
Zanim przedstawię przykład ilustrujący ten temat, muszę wyraźnie zastrzec: opisany poniżej przypadek wydarzył się naprawdę, ale nie należy go łączyć z moim obecnym ani poprzednimi miejscami pracy, choć osobiście miałem okazję go poznać. Z przyczyn oczywistych zostanie on opisany anonimowo.
IT, jak już powiedziałem, jest wszechobecne. W dużych organizacjach każdy proces ma odzwierciedlenie w systemach informatycznych. Jednocześnie od wielu lat obserwujemy procesy konsolidacji firm, a nawet branż, co siłą rzeczy powoduje, że coraz częściej mamy do czynienia z potrzebą integracji systemów IT. Niekiedy jest to realizowane poprzez wdrożenie systemu firmy przejmującej w firmie przejmowanej, ale niekiedy stosuje się rozwiązanie tymczasowe w postaci oprogramowania łączącego dwie różne platformy. A że prowizorki są najtrwalsze, tak było i w tym przypadku.
Miejscem zdarzenia był terminal logistyczny prowadzący operacje o dużej dynamice, w bezpośrednim współdziałaniu z wieloma klientami i przewoźnikami. Terminal kilka miesięcy przed incydentem został włączony w struktury dużej firmy logistycznej, która go nabyła, wraz z kilkoma innymi terminalami w ramach projektu akwizycyjnego. Czas płynął bardzo szybko, co było widać nawet po prędkości jazdy wózków widłowych. Wraz z akwizycją uruchomiono aplikację integrującą system dotychczas używany z systemem nowej firmy. Pracownicy dokładnie znali „stary” system i korzystali z niego bez żadnych problemów.
Zupełnie inaczej sprawa wyglądała z nowym systemem. Pracownicy mieli już „stare” nawyki, co będzie miało duże znaczenie w tej historii. Szybkość działania firmy wpływała także na jakość opracowanego oprogramowania integrującego i jego wdrożenie (nie tylko instalacji, ale również szkoleń pracowników). Niestety pośpiech szybko dał o sobie znać w postaci pierwszej awarii. Oba systemy „padły” i operacje „stanęły”.
Na krótko. IT dość szybko opracowało łatkę i system wrócił do pracy. Sytuacja powtórzyła się jeszcze kilka razy, aż wreszcie system padł na dobre. Koszmar każdej firmy logistycznej zmaterializował się w pełnym wydaniu – towary przyjeżdżają, ale nie można ich „przyjąć w systemie”, więc są rozładowywane, a „przyjęcie” zrobi się później.
To jedna strona medalu. A druga? Skoro nie można przyjąć, to nie można także wydać. I tu ponownie pojawia się presja szybkości – samochody stoją i czekają, czekają także klienci, a kary umowne wiszą w powietrzu. Koszmar się pogłębia. Co robić? Z „pomocą” przyszły stare nawyki. Pracownicy zaczęli wystawiać dokumenty WZ w edytorze tekstu (sic!). Nie wszyscy wiedzieli, że trzeba nadać tym dokumentom numer. A wciąż słychać: „szybciej, szybciej, jeszcze szybciej”, bo przecież są już godziny zaległości. Była ogromna presja, w efekcie nienumerowane WZ-ki mnożyły się. A skoro tak, to wcześniej czy później musiało dojść do wystawienia dwóch takich samych WZ-tek. I doszło. Wystawiono, załadowano, wywieziono, ale gdy drugi transport dojechał, klient przyjął go, nie mówiąc, że dostał powtórnie to samo. Skoro jeden dostał dwa razy to samo, to dla następnego klienta zabrakło. Na półce jest „zero”, mimo że w systemie jest „ileś” I teraz dopiero sprawa trafia do szefa bezpieczeństwa z informacją, że coś zginęło.
W taki to sposób zły system IT i złe nawyki zablokowały operacje logistyczne. Do czasu incydentu security manager nie był w ogóle angażowany w kwestie IT, a mniejsze (krótkotrwałe) awarie nie były nawet postrzegane ani jako problem security, ani problem ciągłości działania.
Rozwiązanie takiego problemu nie jest łatwe i z pewnością proste narzędzia tu nie zadziałają. Każdy obiekt musi go rozwiązać indywidualnie, adekwatnie do swoich procesów, struktury, narzędzi itd. Problem ten pokazuje jednak, że IT, security i pion operacyjny powinny pracować wspólnie. W ten sposób być może dałoby się uniknąć dużego problemu.
„Kreatywność” – czy jeden człowiek może zablokować logistykę?
Ta historia wydarzyła się w dużej fabryce mebli, w jej centrum logistycznym, w którym są magazynowane zarówno surowce, jak i wyroby gotowe.
Surowiec…
Surowce i komponenty produkcyjne dość często są traktowane jak mienie mniejszej wartości. Ich wartość w stosunku do wyrobu gotowego jest faktycznie mniejsza, ale znaczenie – niekoniecznie. Znaczenie surowców jest duże, wszak to z nich powstają wyroby gotowe. Przykładowym surowcem jest obrzeże meblowe, czyli taśma naklejana na brzeg stołu czy półki. Do oklejania płyt meblowych stosuje się maszyny, dlatego obrzeże jest dostarczane w rolkach. Ale skoro jest rolka, to pojawiają się jej wymiary. Maszyna z reguły ma określoną średnicę rolki, a to oznacza, że długość obrzeża w rolce może być różna, zależnie od jego grubości.
To właśnie wykorzystał pewien magazynier, przypisując rolkom stałą długość obrzeża (sic!). Reszta była już prosta. Bez wdawania się w szczegóły „zaoszczędzone” przez magazyniera obrzeże lądowało… w warsztacie stolarskim szwagra naszego „bohatera”. Pewnego dnia magazynier zachorował. Na zastępstwo przyszedł ktoś inny i wtedy okazało się, że to, co jest w systemie, nie ma odzwierciedlenia na półce magazynowej i brakuje obrzeża, które właśnie jest potrzebne. Szef produkcji szybko zareagował, przestawiając produkcję, i w ten sposób zapobiegł poważnemu problemowi. Jednak jeden człowiek o mały włos nie zatrzymał produkcji w dużej fabryce.
Produkt…
Każdy magazyn ma swoją dynamikę, z reguły dużą. Tu wszystko dzieje się szybko, więc czasami to i owo może się nie udać. Tak było z pewnym operatorem wózka widłowego, który „nie trafiał” w paletę, zamiast czego „trafiał” w paczki z meblami, uszkadzając je. Bojąc się konsekwencji braku profesjonalizmu, każdą paletę z uszkodzonym opakowaniem układał na górze regału magazynowego. Długo nic się nie działo. Wiadomo że produkcja może rozminąć się z zamówieniami, więc w magazynie jest pewna nadwyżka wyrobów, która w wyniku sprzedaży z czasem maleje. Tak było i tym razem, wprawdzie przeprowadzono okresową inwentaryzację, ale, jak się dowiedziałem, „na podstawie danych w systemie”. W praktyce oznaczało to porównanie „wejścia” z „wyjściem”. A stan magazynu? Skoro „wejście” i „wyjście” są znane, to znaczy że w magazynie jest różnica – stwierdził rozbrajająco mój rozmówca.
To był jeden z tych momentów w moim życiu zawodowym, kiedy zaniemówiłem zupełnie. Takie postępowanie operatora doprowadziło do sytuacji, że ten sam szef produkcji, który sprawnie zadziałał w przypadku obrzeża, nie planował produkcji mebla, na który przychodziły zamówienia, bo… miał nadwyżkę. Jednak gdy przyszło do wysyłki, okazało się, że na półce mebli nie ma. Trzeba było wyjaśnić, dlaczego i gdzie są te, które widniały w systemie. Pierwsze podejrzenie dotyczyło kradzieży. Praca nie szła łatwo, choć początek był łatwy – wszyscy mówili prawdę, nawet operator wózka widłowego. W końcu ładował na regał to, co miał. To prawda, chociaż nie cała.
W pewnym momencie nastąpił jednak impas. W wyjaśnieniu pomógł przypadek. Nieprzychylny szef magazynu – chyba na złość – przydzielił mi niewygodne miejsce pracy, skąd zauważyłem coś zagadkowego. Gdyby nie to miejsce, pewnie miałbym dużo trudniej…
Życzę wszystkim koleżankom i kolegom
Szczęśliwego Nowego Roku.
1) ISO 28000 – System Zarządzania Bezpieczeństwem Łańcucha Dostaw. 2) PN-EN ISO 9001 Systemy zarządzania jakością – Wymagania. 3) PN-EN ISO 14001 Systemy zarządzania środowiskowego – Wymagania i wytyczne stosowania. 4) PN-EN ISO 22300 Bezpieczeństwo i odporność – Terminologia. 5) PN-EN ISO 22301 Bezpieczeństwo powszechne – Systemy zarządzania ciągłością działania – Wymagania. 6) PN-EN ISO/IEC 27001 Technika informatyczna – Techniki bezpieczeństwa – Systemy zarządzania bezpieczeństwem informacji – Wymagania. 7) PN-ISO 45001:2018-06 Systemy zarządzania bezpieczeństwem i higieną pracy – Wymagania i wytyczne stosowania. 8) Customs Trade Partnership Against Terrorism. 9) Autoryzowany Operator Ekonomiczny. 10) ISO 3700 System zarządzania działaniami antykorupcyjnymi – Wymagania i wytyczne do stosowania. 11) https://www.ft.com/content/9299de8e-0e17-11e0-86e9-00144feabdc0 12) https://www.radio.rzeszow.pl/wiadomosci/17277/to-nie-alarm-rcb-falszywe-smsy-trafily-do-mieszkancow-podkarpacia
Jacek Grzechowiak
Menedżer ryzyka i bezpieczeństwa. Przez kilkanaście lat związany z grupą Securitas, obecnie w grupie Celsa.
Absolwent WAT, studiów podyplomowych w SGH i Akademii L. Koźmińskiego. Gościnnie wykłada na uczelniach wyższych.